NEWS CENTER
Fabric Classroom | Classification and Formation of Woven Fabrics, and Woven Process Flow!
2022-11-22
Fabrics are products made of yarn (thread) or fiber, mainly including woven fabrics, knitted fabrics and non-woven fabrics. The product made of two groups of mutually perpendicular yarns (threads) interwoven on the loom is called woven fabric, such as plain cloth, gabardine, khaki, satin, etc. Yarns arranged along the length of the fabric are called warp, and those arranged along the width of the fabric are called weft. Changing the raw materials, thickness and structure of the yarn, or using different colors of yarn to cooperate with each other, and different warp and weft yarns interweave with each other, you can weave fabrics of different styles and purposes. These fabrics can be divided into clothing fabrics, decorative fabrics and industrial fabrics according to their uses.
01
Woven fabrics and their classification
Fabrics are products made of yarn (thread) or fiber, mainly including woven fabrics, knitted fabrics and non-woven fabrics. The product made of two groups of mutually perpendicular yarns (threads) interwoven on the loom is called woven fabric, such as plain cloth, gabardine, khaki, satin, etc. Yarns arranged along the length of the fabric are called warp, and those arranged along the width of the fabric are called weft. Changing the raw materials, thickness and structure of the yarn, or using different colors of yarn to cooperate with each other, and different warp and weft yarns interweave with each other, you can weave fabrics of different styles and purposes. These fabrics can be divided into clothing fabrics, decorative fabrics and industrial fabrics according to their uses.
one
Classification of woven fabrics for clothing
The woven fabrics for clothing are often classified according to the type of raw materials, whether the yarn is bleached and dyed, fabric pattern and width.
1. Classification according to the type of raw materials
(1) Pure textile: The warp and weft yarns are all made of the same fiber material, such as cotton fabric, linen fabric, wool fabric, silk fabric, etc.
(2) Blended fabric: warp and weft yarns are fabrics made of two or more kinds of fibers, such as polyester/cotton fabrics, wool/polyester fabrics, polyester/linen fabrics, wool/polyester/nitrile fabrics and medium length fabrics.
(3) Interleaved fabric: fabric made of different raw materials of warp and weft, such as silk wool interweave, cotton and viscose filament interweave, silk and viscose filament interweave, etc.
(4) Interleaved fabric: A fabric made of warp and weft yarns made from two or more different materials and combined into strands.
2. Classification according to whether the yarn is bleached
(1) Natural color fabric: Yarns are processed into fabrics without bleaching and dyeing, and then sold directly or processed into finished products through printing and dyeing.
(2) Yarn dyed fabric: Fabrics made from dyed and bleached yarns.
3. Classification according to fabric pattern
(1) Plain fabric: The fabric without pattern, such as plain cloth, twill cloth, satin fabric, etc.
(2) Small pattern fabric: through the change of fabric structure, small pattern fabrics are formed on the fabric, such as various tweeds.
(3) Jacquard fabric: A fabric with a wide range of patterns formed by controlling a single warp, such as flowered soft satin.
4. According to fabric width, it can be divided into wide fabric, narrow fabric and belt fabric.
two
Classification of decorative woven fabrics
There are many kinds of decorative fabrics, which are often divided according to their uses.
(1) Bedding: such as quilt cover, quilt cover, bed sheet, towel and quilt, pillow towel, etc.
(2) Furniture cloth: such as sofa cover, chair cover, etc.
(3) Indoor articles: such as curtain cloth, wall covering cloth, carpet, curtain fabric, etc.
(4) Restaurants and toiletries: such as tablecloths, towels, bath towels, etc.
three
Industrial woven fabrics
Industrial woven fabrics are increasing with the development of the industry. The woven fabrics used in various industries are listed as follows:
(1) For primary industry: such as agricultural hose, fishing canvas, tarpaulin, etc.
(2) For the secondary industry: such as tire cord cloth, conveyor belt, geotextile for building roads and dams, various rubber underlays, filter cloth, screen mesh, paper blanket, etc.
(3) For the tertiary industry: parachute cloth, artificial blood vessel, etc.
02
Formation of woven fabrics
Woven fabric is made by weaving warp and weft yarns on the loom according to the requirements of fabric organization.
Figure 1-1 is a schematic diagram of plain weave fabric woven on a loom. The warp (1) is led out from the weaving shaft (2) behind the loom, wound around the back beam (3), passed through the yarn splitting hinge (4), passed through the heald eyes (6) and (6) on the heald frame (5) and (5) respectively according to certain rules, and then passed through the reed teeth of the reed (7), and interweaved with the weft yarn at the weaving mouth to form a fabric. Under the action of the loom take-up mechanism, the formed fabric bypasses the breast beam 8, the pricking roller 9 and the cloth guide roller 10, and finally is wound on the cloth winding roller 11.
When the loom is running, heald frames 5 and 5 'respectively move up and down in a vertical direction, dividing the warp yarn into upper and lower pieces to form a shed. When the shuttle 12 passes through the shed, the weft yarn is unwound from the bobbin 13 installed in the shuttle, leaving a piece of weft yarn in the shed. When the heald frame moves in the opposite direction, the upper and lower warp yarns exchange positions to clamp the weft yarn. At the same time, the reed 7 swings forward to the loom, pushing the weft yarn to the loom mouth, and the warp yarn and the weft yarn interweave at the loom mouth to form a fabric. Every time the main spindle of the loom rotates, a new shed is formed, and a new weft yarn is introduced to complete a beating up motion. In this way, the weaving process of continuous production is formed.
It can be seen that the formation process of fabric on the loom is completed by the following processes and movements.
(1) According to the law of warp and weft interweaving, the warp is divided into upper and lower pieces to form the shedding motion of the shed.
(2) The motion of inserting the weft into the shed.
(3) The beating up motion of pushing the weft yarn introduced into the shed to the loom.
(4) The coiling motion that pulls the fabric away from the fabric forming zone.
(5) Let out the warp from the loom and feed it into the let off motion of the work area.
The above movements are completed by the corresponding mechanism of the loom. In addition, in order to improve product quality, ensure safe operation, improve production efficiency and the adaptability of the loom, the loom is also equipped with various auxiliary mechanisms, which can automatically fill the weft, stop the warp yarn breaking, stop the weft yarn breaking, and make multi-color weft weaving and protective devices. On the new shuttleless loom, with the wide application of computer, electronics and other high-tech, the level of loom integration, automation and high-speed has been greatly improved.
03
Weaving process flow
In the process of fabric weaving on the loom, the warp shall bear the effects of periodic tensile, impact and bending loads. Under the effects of these external forces, the structure of the warp may be damaged. If the strength and elasticity of the warp are insufficient to withstand the effects of these external forces, yarn breakage will occur. In addition, the warp is subject to repeated friction of the warp stop piece, heald and reed, which is very easy to hairiness and pilling. If the warp is worn seriously, it will also cause warp breakage. Therefore, in order to reduce the warp yarn breakage and improve the weaving performance of the yarn, it is necessary to try to cling to the warp yarn hairiness before weaving, reduce its friction coefficient, increase the strength of the warp yarn and ensure that the warp yarn has enough elasticity. The working conditions of the weft yarn on the loom are different from those of the warp yarn. The weft yarn is mainly affected by the weft insertion tension. Its size mainly depends on such factors as the weft insertion speed, the weft yarn package form, the size of the unwinding balloon and the weft yarn braking force. The tension on the weft is a one-time load. On the shuttle loom, because of the low weft insertion speed, the peak value of the weft tension is smaller than the warp tension. Therefore, the yarn with lower strength and twist can be used as the weft. But on the high speed shuttleless loom, because of the high weft insertion speed, the weft yarn should have high strength to meet the requirements of weaving.
In addition, before weaving, the yarn must also be wound into a package with a certain shape, size, good shape and reasonable structure. For example, the warp yarn is wound into a weaving shaft, and the weft yarn is wound into a bobbin or bobbin to meet the weaving needs.
It can be seen that warp and weft must go through a series of preparation processes before weaving. These processes are collectively referred to as preparatory works before weaving.
The main task of warp preparation is to improve the strength and wear resistance of the yarn, eliminate yarn defects and impurities on the yarn, improve the weaving performance of the warp, and wind the warp into the package required by the process design. The main task of weft preparation is to remove the coarse and fine knots and other yarn defects and impurities on the yarn, and wind them into a certain size of fiber or Jane. In the production of some low-grade fabrics, the weft yarn does not need to be prepared before weaving. Generally, the tube yarn produced by the spinning machine can be directly used as the fiber, which is called direct weft yarn. The knots used in some medium and high grade fabrics are called indirect weft yarn. After the impurities and defects of the tube yarn produced by the spinning machine are removed, the tube yarn is rewound on the weft winding machine to form a filament to improve the knot quality. In some cases, in order to stabilize the twist of the weft yarn and properly improve the strength of the weft yarn, weft yarn also needs to be wet and twisted.
Shuttleless looms have high weft insertion speed and large change of acceleration value during weft insertion, which will inevitably cause a sudden increase of weft tension in the process of weft insertion. Therefore, weft insertion without shuttle has higher requirements on weft strength, package form and package structure.
Due to the different raw materials, varieties and uses of fabrics, the preparation process before weaving is also different, which makes the weaving and production process of different fabrics, such as cotton grey cloth, yarn dyed fabric, wool fabric, silk fabric, hemp fabric and synthetic fabric, different.
one
Batch Warping and Sizing Process
This process is mainly applied to the production of cotton parison fabric, ramie fabric, spun silk fabric, etc. Generally, batch warping is adopted. The sizing process has a large batch of products, most of the fabric structures are relatively simple, and some simple striped yarn dyed fabrics can also be produced by this process. The process flow is shown in Figure 1-2.
two
Process flow of sectional warping
The sectional warping process is mainly applied to the production of fabrics with many varieties of patterns and colors, such as wool fabrics, silk fabrics, yarn dyed fabrics and cotton fabrics, and the product batch is small. The process flow is shown in Figure 1-3.
Due to different raw materials and different products, in preparation for processing, the wool fabrics and colored fabrics with ply yarn as warp and weft yarn must first go through the processes of doubling, twisting, winding, steaming and fixed twisting, etc. The original yarn of the spun fabric is processed into ply yarn, the colored yarn is used as warp and weft yarn, the original yarn must go through the processes of bleaching and dyeing, the silk fabrics with natural silk or chemical filament yarn as warp or weft yarn, and the synthetic filament fabrics, It is necessary to go through such processes as impregnation, merging, twisting, and fixed twisting. Sizing of synthetic filament often adopts the process of merging after sizing, which will not be listed here. However, the preparation of all kinds of fabrics generally goes through the following processes.
1. Winding
In the textile industry integrating spinning and weaving, most of the yarn for weaving is sent from the spinning department to the weaving department in the form of tube yarn. As the yarn capacity of tube yarn is small, if it is directly used for warping, the tube change times will be very frequent, which will cause the warping machine to stop frequently, reducing the production efficiency of the machine. In addition, there are inevitably some impurities and various yarn defects on the tube yarn that affect the appearance quality of the fabric. Therefore, it is necessary to go through the winding process to wind the tube yarn with small capacity into a much larger package yarn with proper density and good shape, and at the same time remove the defects and impurities on the yarn. When weaving on shuttleless looms, it is also required to wind the weft yarn into a package yarn with good shape and reasonable structure.
The quality of winding has an important influence on the subsequent process. Therefore, the requirements for winding process are:
(1) The yarn shall be wound into a package with large capacity, reasonable structure and good shape, and the winding tension and density shall be appropriate and uniform to facilitate transportation and storage.
(2) Under the condition of not damaging the original physical and mechanical properties of the yarn, the defects and impurities on the yarn shall be removed as far as possible.
(3) Ensure that the joint quality meets the requirements.
2. Warping
The task of the warping process is to wind a certain number of packages evenly and parallel on the warp beam or weaving beam according to the length, arrangement sequence, width, etc. specified in the process design, according to the requirements of the process design, for sizing or threading process.
Warping quality is of great significance to the smooth progress of sizing process and fabric quality. Therefore, the warping process must meet the following process requirements.
Warping methods commonly used in textile mills can be divided into batch warping and sectional warping according to their technological characteristics.
Batch warping is to divide the total warp yarns required for the full width fabric into several batches according to the number of warp yarns, wind them on several warp shafts (the number of warp yarns on each warp shaft should be equal as far as possible), and then size or wet these warp shafts on the sizing machine, and wind them into weaving shafts meeting the weaving requirements according to the specified length. This warping method is applicable to the warping of large quantities of primary color fabrics. Its advantages are fast speed and high efficiency, while its disadvantages are more yarn recovery.
Splitting warping is to divide the total warp yarn required by the full fabric into several strips according to the capacity of the simple sub frame and the arrangement of colored yarns, wind these strips on the warping roller in parallel according to the width and length specified by the process, and then rewind all the strips on the weaving shaft at the same time. Warps with sectional warping generally do not need sizing. The advantage of this warping method is that it is conducive to the arrangement of colored yarns or warp yarns of different quality and structure, with less filament return, and the disadvantage is that the production efficiency is low. It is mainly applicable to warping of small batch, multi variety yarn dyed fabrics, wool fabrics, silk fabrics, towel fabrics and other fabrics.
(1) The single yarn tension and the whole piece warp tension should be consistent and even as far as possible.
(2) The arrangement and winding density of warp yarns on the warp beam shall be uniform, and the warp beam shall be rounded and well formed.
(3) The number, length and yarn arrangement order of warping are strictly in line with the process requirements.
(4) The joint quality meets the specified standards, with less wire return and high production efficiency.
3. Sizing
The task of the sizing process is to size the warp on the sizing machine, combine the warp yarns of several warp shafts according to the total number of warp yarns required for the whole fabric, and wind the warp yarns after sizing into a weaving shaft. Its purpose is to make the yarn hairiness cling, improve the yarn strength and abrasion resistance, keep the original elastic elongation of the yarn as far as possible, and improve the warp weaving performance.
Sizing is an important process in warp preparation engineering. Sizing quality has great influence on weaving production. If the sizing process is reasonable and the quality is good, the weaving can achieve the goal of high yield, high quality and low consumption; On the contrary, it will bring great difficulties to weaving.
Sizing is generally carried out on the sizing machine to make the warp pass through the specially made sizing solution. After being dipped, rolled and dried, part of the sizing solution is coated on the surface of the yarn body to form a tough sizing film, which makes the hairiness stick, and the yarn smooth and wear-resistant; The other part of the size permeates into the interior of the yarn, making the fibers adhere to each other and increasing their cohesion, forming a firm size film, thus improving the breaking strength of the yarn.
Warp sizing has strict requirements on the size, size and sizing process used. The size film should be flexible, firm, smooth and elastic, and should ensure that it meets the sizing rate, moisture regain and elongation required by the process design.
4. Warp and weft preparation
Warp tying is the last process of warp weaving preparation. Its task is to thread all the warp yarns on the weaving shaft into the warp stop, heddle eyes and reed teeth according to certain rules according to the requirements of the fabric process design, so that the shed can be formed during weaving and the required fabric can be woven, and the warp yarn can be stopped in time when it is broken without causing weaving defects.
The quality of warping has a direct impact on whether weaving can be carried out smoothly and whether the product quality meets the requirements. If there is a mistake in warp threading, the required warp density and width of the fabric may not be woven. Therefore, it is necessary to wear the warp in strict accordance with the requirements.
The purpose of knotting and threading is the same, but the method of knotting is completely different from threading. By knotting, the remaining warp yarns on the loom are connected one by one with the warp yarns on the weaving shaft to be used, and then all the warp yarns on the loom are pulled through the warp stoppers, heald holes and reed teeth to meet the same requirements as the warp threading. It is very convenient and fast to use warp knitting method to weave the same kind of fabric with complex weave.
Weft preparation includes winding, weft winding, hot and wet set twisting and other processes. The winding cylinder can wind the weft yarn into a bobbin required by the shuttleless loom, and the weft winding is to wind the weft yarn into a bobbin suitable for weaving on the shuttleless loom, so as to facilitate weaving. The hot wet fixed twist is used to fix the twist of the weft yarn and prevent the weft yarn from shrinking and looping during weaving.
After the fabric is woven on the loom, it also needs to pass the inspection and finishing processes such as cloth inspection, cloth folding, repair and baling. In areas with high relative humidity, the cloth drying process is required to prevent the products from mildewing and deterioration during storage and transportation. In order to reduce neps, impurities and improve the appearance of some commercially available primary color cotton fabrics
Service hotline
Mr Huang
Whatsapp/ Mobile:0086-13697459643
E-mail: allias_chen@yahoo.com
Address: No. 2 Industrial Park, Quannan County, Ganzhou City, Jiangxi Province, China
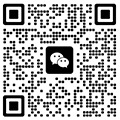
Follow us
Copyright© 2022 Quannan Haixu Fiber Products Co., Ltd Powered by www.300.cn SEO